✆ + 1-646-235-9076 ⏱ Mon - Fri: 24h/day
Today’s cloud-based Industrial Internet of Things (IIoT) platforms have changed everything
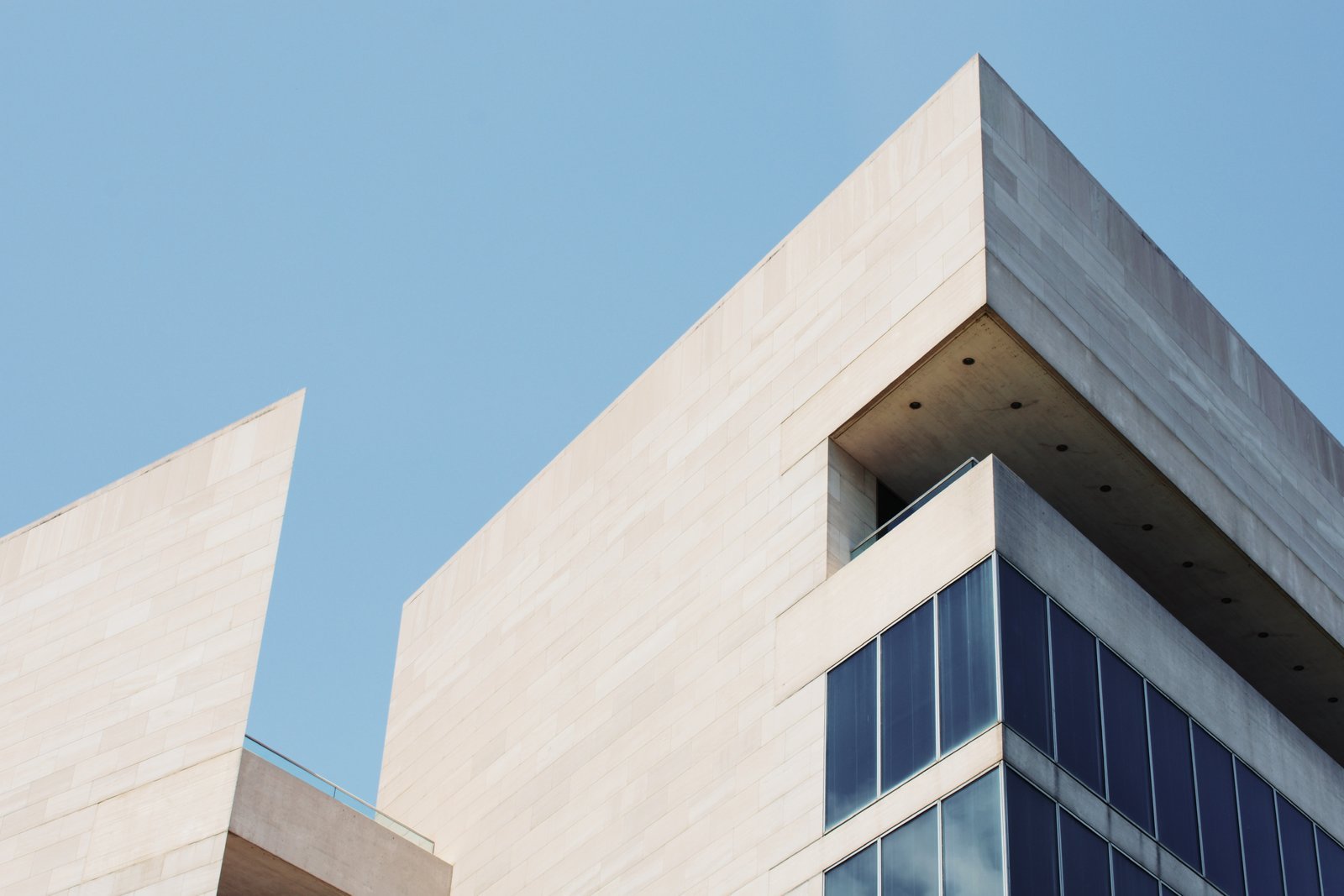
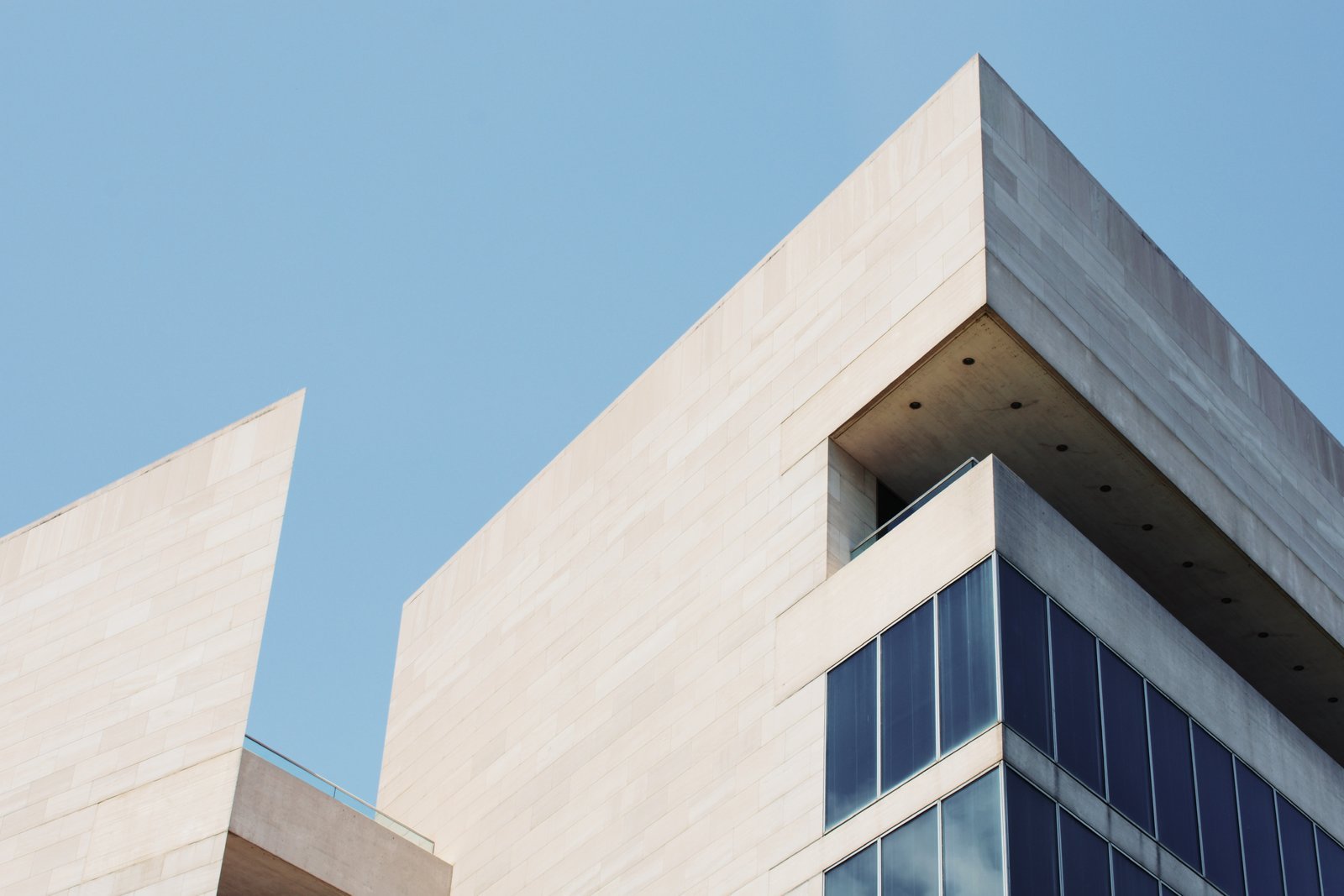
Data collection in manufacturing is a valuable asset for organizations to optimize their processes and better understand how their productions lines are operating but it has to date been very limited in scope. In previous times, data was gathered from a piece of equipment and scrutinized for areas of improvement. Think of it as thousands of employees continuously running around collecting data on clipboards and manually feeding that information into an analysis tool; a lengthy and tiresome process.
Thankfully, today’s cloud-based Industrial Internet of Things (IIoT) platforms have changed everything. There is no longer a barrier between discrete data points or individual application intelligence. Instead, good count data can be used to improve OEE while also reducing loss and waste. That same data set can also improve production efficiency and compare the difference between production shifts.
However, all this potential doesn’t mean your organization wants – or needs – to invest in all-new sensors, networking solutions, or data-gathering devices. A better approach is to leverage what you already have whilst leveling it up with the latest IIoT protocols; the aim being to build a feedback loop for all actionable data.
How does the IIoT drive efficiency and innovation?
First, let’s take a closer look at the myriad of powerful impacts that IIoT technology can have in a typical manufacturing setup.
Fundamentally, the IIoT enables different devices from across the manufacturing environment to automatically communicate with each other – even if they use different proprietary protocols that never included 24/7 monitoring access. Companies looking to connect devices from disparate manufacturers can now choose advanced HMIs, protocol converters, and other automation products that natively speak different protocols. These industrial products then enable devices to communicate regardless of the physical medium and offer industrial fluency and multi-protocol support.
In turn, this enables the IIoT to ensure operational efficiencies across the entire manufacturing infrastructure. One such efficiency involves using data collected from monitoring points along a manufacturing line to minimize waste and downtime. As technology continues to improve, these status points will include an increased volume of information from a wider range of sources. Managed Ethernet switches will be able to report on the flow of data throughout the facility in the same way that sensors on assembly lines can report a product’s status on a production line.
This expanded collection of operational data enables organizations to make actionable data for a wide range of stakeholders by using visual management solutions to display critical performance data in real-time. In turn, different personnel from within the organization can gain granular visibility into operations, driving productivity and increasing throughput. And from there, the concept can be extended to include the supply and distribution chain to present a comprehensive view of the entire operation.
How should you choose IIoT products and services?
With all these business benefits to be harnessed, it is little wonder that more and more manufacturing and industrial organizations are seeking to deploy IIoT ecosystems. But what are the key considerations they should bear in mind?
First, think about protocol conversations. Gathering data in industrial environments typically involves the interoperability of numerous devices employing different and incompatible protocols. To ensure a solid Industrial Internet of Things (IIoT) foundation, a protocol conversion gateway is vital to meeting end-host requirements for the delivery of data between different components. This streamlines network operations increases network performance and extends legacy equipment investment.
Security is another key consideration. Traditionally in manufacturing and industrial environments, it has meant physical isolation of automation equipment and enterprise networks. If nothing is connected to automation equipment, the threat of security breaches is fairly low. However, the IIoT means that connection-free facilities are increasingly few and far between. As they embrace this new reality, security must be addressed through careful network planning and the use of IP address best practices.
There are a few different options: routers can be deployed within a network to limit network traffic to specific types of traffic or to specific users; Network Address Translation (NAT) can be used to obscure devices on the network from inbound access; and VPNs or tunneling appliances can make factory-to-factory, supply chain-to-factory, or factory-to distributor communication secure by creating virtual “tunnels” through which sensitive data can be transmitted.
Next, consider visual data management. This can be broken down into three easy steps: connect to equipment, collect the data, and display the results. By providing immediate access to data that is consistent, easily understood, and easily seen, employees remain aware of where processes currently stand and where they need to be, promoting employee ownership to achieve the desired objectives, thereby refining processes and driving productivity while fostering employee pride in a job well done.
As the number of critical assets being deployed in the field rises, the need for flexible, secure remote site process control and monitoring without expensive network infrastructures increases in pace. By pushing control to the network’s edge, organizations add more than operational reliability—the secure automation of field processes improves the speed and accuracy of operations while helping to reduce costs. Ultimately, today’s floor communication protocols should be able to transmit data in a cloud environment, even when network connections are constantly dropped. They should also offer consistent, robust security and easy scalability. The cellular network medium is proving to be highly reliable and secure, offering traditional data encapsulation like VPN tunnels, as well as more advanced methods to secure data like private access point names (APNs) or software-defined networking (SDN).
Fordewind.io is an IoT engineering and development company based in Kyiv, Ukraine. Our main areas of interest and expertise are the automotive industry and Smart Home/City projects. Contact us right now without a doubt and learn more about how we can help you build the future.